LSR Injection Molding
What makes us different?
With more than 15 years of experience in LSR molding service
We have established long-term partnerships with many companies.
We have more than 10 liquid silicone molding machines to provide mass production services and shorten the production cycle.
We have professional cleanrooms and are ISO13485 certified. Provide a strictly hygienic production environment for medical devices and precision electronic components
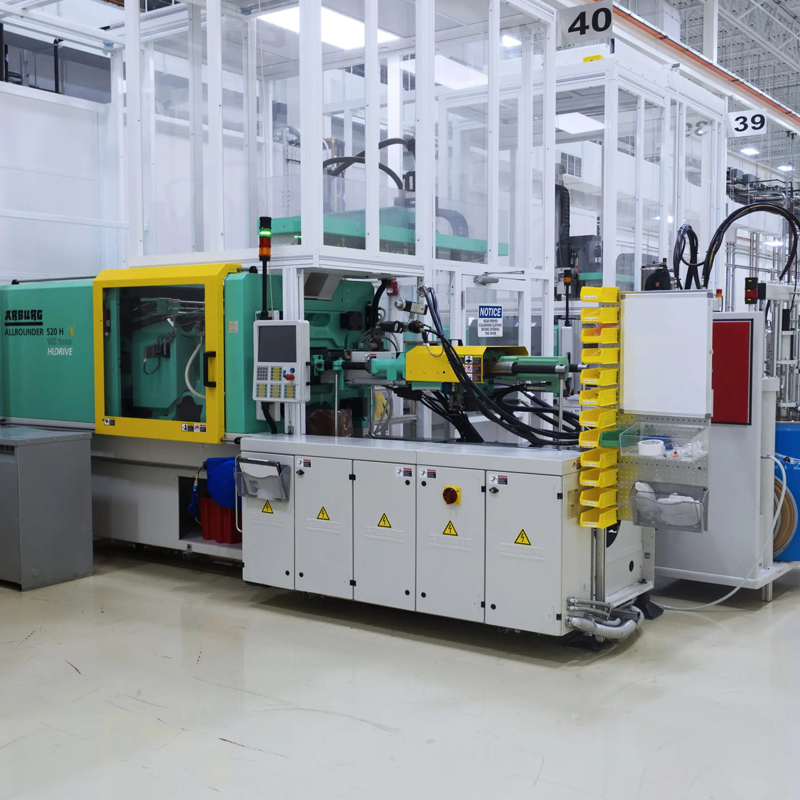
What Is Liquid Silicone Rubber Molding?
The LSR (Liquid Silicone Rubber) molding process consists of two main components: A (matrix) and B (catalyst). These two substances are injected directly into a closed mold, where they mix and start to cure into the exact shape of the part. Once the curing process is finished, the machine ejects the completed part.
This method allows for the large-scale production of silicone products, with fully automated operations in an ISO Class 8 clean room. It is suitable for meeting the requirements of both food-grade and medical-grade industries. Here are the steps involved in customizing silicone rubber products using the LSR molding process.
Advantages of Silicone Injection Molding
Waste Reduction
Our high-precision liquid silicone injection machines can precisely control the injection volume, minimizing raw material waste. Flashing is also effectively managed, reducing the need for additional trimming work after molding.
Ideal for High Precision Applications
LSR injection molding is optimal for producing complex and micro-sized components. The feeding system of the LSR machine can precisely control the amount of silicone with an accuracy of ±0.01g, ensuring strong dimensional stability. These capabilities make LSR injection molding widely applicable for manufacturing seals, membranes, and other intricate components.
Versatile Processing Capabilities
LSR injection molding can achieve single-shot molding, micro molding, and overmolding. Products created through this process exhibit stronger bonding and better flash control, meeting various processing needs.
ISO Class 8 Cleanroom Production
The LSR molding process involves directly injecting raw materials into pre-made molds, allowing for automated production without exposure to external environments. This minimizes waste during production. Our ISO Class 8 cleanrooms provide a stringent hygienic production environment, ideal for medical products and high-precision electronic components.
LSR Injection Molding Process
1. Raw Material Preparation
The process begins with the preparation of the liquid silicone rubber (LSR) material. This involves mixing LSR with a silicone crosslinker and silicone-based fillers to create a uniform LSR compound.
2. Injection by Molding Machine
The prepared LSR compound is fed into the hopper of an injection molding machine. The machine heats the compound and injects it into the mold cavity with precision.
3. Mold Filling and Curing
Once in the mold cavity, the LSR compound rapidly fills the space and cures due to its heat-reactive properties, forming a solid silicone rubber product.
4. Cooling and Demolding
After curing, the mold is cooled to stabilize the silicone rubber. Once cooled, the mold is opened, and the solidified silicone product is carefully removed.
5. Trimming and Quality Inspection
The extracted silicone rubber product may require trimming to remove any excess material or flash. The product then undergoes a thorough quality inspection to ensure it meets all design specifications and standards.
6. Post-Processing
For specific applications, additional post-processing steps such as surface coating, printing, or bonding may be necessary to finalize the product.
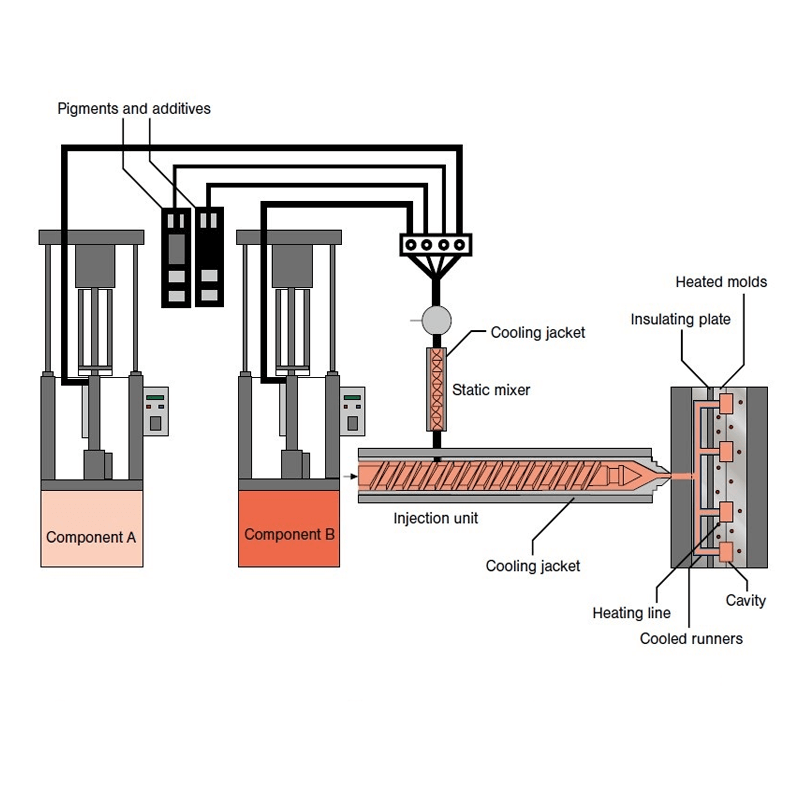
Liquid Injection Molding Capabilities
Single-Shot Molding
A single LSR material is utilized to manufacture silicone products in this molding process. This method is ideal for producing baby and medical items, such as pacifiers and silicone braces, ensuring high standards of safety and quality.
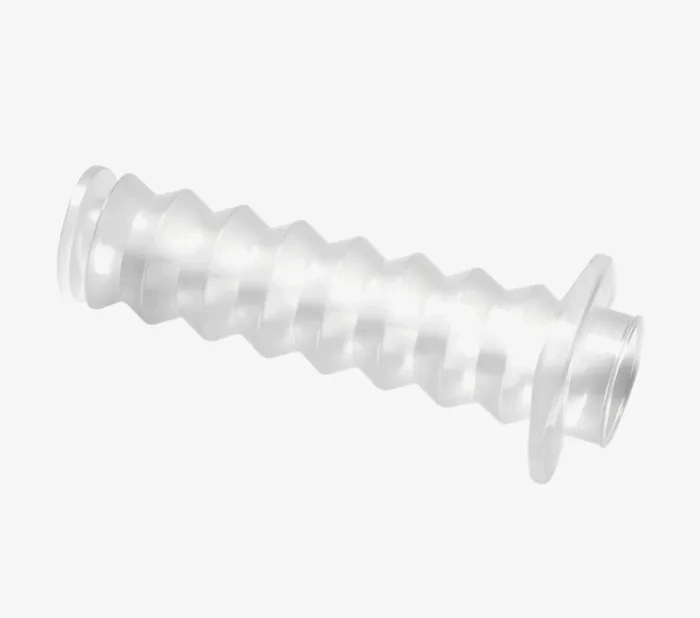
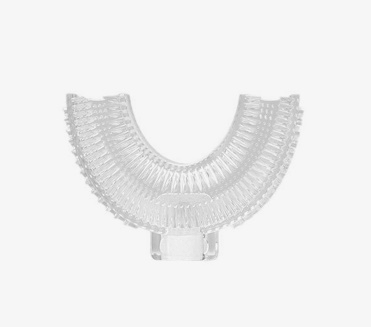
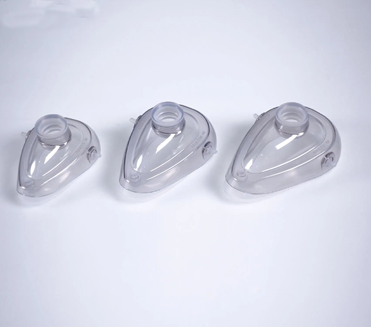
Micro Injection Molding(Complex)
The LSR molding process is capable of producing small and intricate parts with an injection volume of less than 1 gram. These micro silicone components are commonly used in electronic products, such as SIM card holders and earplugs.
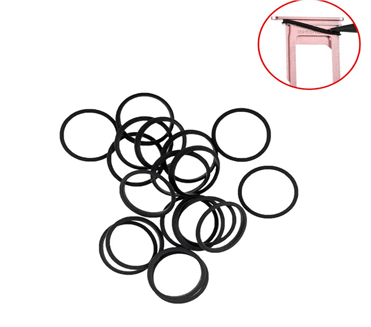
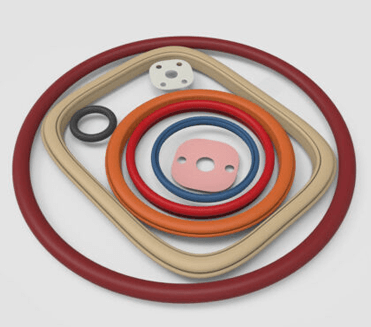
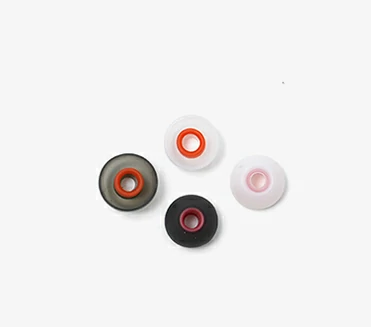
Silicone Overmolding
LSR can be combined with various polymers, including plastics, metals, and fabrics. This versatility makes it ideal for producing sealing components in electronic products, such as electronic connectors and other critical parts.
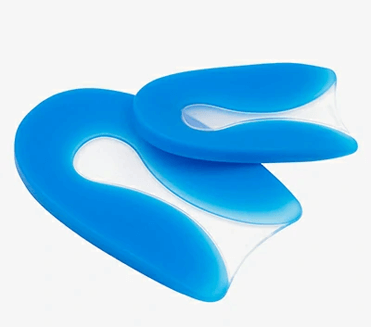
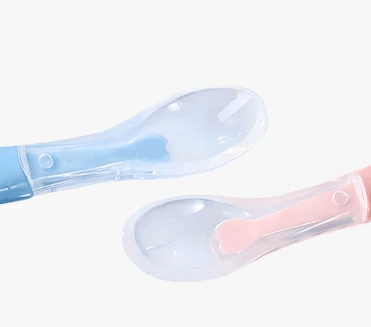
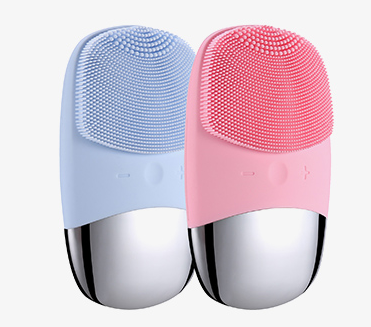
Related Custom Solutions from Siliconebase
Single-shot molding
In this molding process, only one LSR material is used for injection molding parts.
Multi-shot molding
LSR is combined with two or more polymers or a polymer and substrate in this process for more complex components.
Overmolding
In overmolding, the liquid silicone rubber is molded around a substrate or finished component
Hygienic molding
LSR parts are produced in a clean, hygienic environment that are highly-controlled to various levels, such as white rooms or more stringent ISO cleanrooms with various classifications.
Applications of LSR (Liquid Silicone Rubber) Injection Molding
LSR injection molding technology is extensively utilized across various industries, including:
Used for manufacturing silicone seals, tubes, artificial organs, and other medical components.
Automotive Industry
Ideal for producing seals, sound-dampening materials, cushioning pads, and other automotive parts.
Electronics and Electrical
Employed in creating electronic seals, electrical insulation components, and conductive parts.
Perfect for crafting safe and comfortable nipples, bottles, and breastfeeding devices.