What Is Overmolding & Insert Molding
Overmolding and insert molding are two distinct injection molding techniques utilized in the production of commercial and industrial products. Both processes involve molding a plastic component over an existing part, but they differ in terms of the properties and functions of the underlying component, leading to varied applications.
Misunderstanding these processes can result in several issues, including product failure, material waste, and increased production costs. We will provide a comprehensive comparison of insert molding and overmolding to guide you in selecting the most appropriate technique for your project.
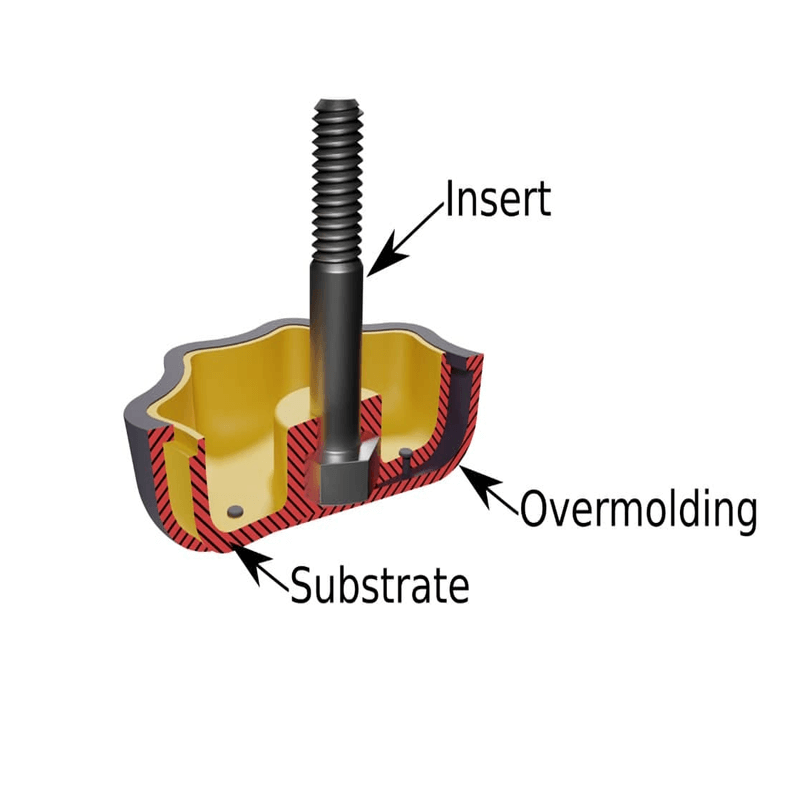
Why Choose Overmolding and Insert Molding?
We specialize in high-performance Liquid Silicone Rubber (LSR) and injection molding products. Injection molding involves injecting molten material into a mold, shaping it under high temperature and pressure, and then cooling and ejecting the component. Our precision molds enable the efficient production of thousands of identical, high-quality parts.
Protection and Durability
Overmolding integrates elastomeric materials, such as silicone and rubber, with other substrates to meet diverse application needs:
- Soft Touch: Enhances grip and comfort with a soft, tactile surface.
- Anti-Slip: Ensures secure handling and minimizes slippage.
- Waterproofing: Creates effective seals and gaskets for electronics and automotive applications.
- Insulation: Provides excellent electrical insulation for components requiring isolation.
- Vibration Dampening: Absorbs vibrations, improving durability and longevity in electronic, automotive, and industrial environments.
Design Flexibility
The overmolding process offers extensive customization options to meet specific requirements, including enhanced strength, durability, waterproofing, sealing, corrosion resistance, or electrical conductivity. This flexibility allows for tailored solutions across a wide range of applications.
Enhanced Functionality
By incorporating electronic connectors, threaded inserts, or bearings into plastic components, overmolding significantly boosts the overall strength and load-bearing capacity of the part. This integration makes components suitable for more demanding applications.
Cost Efficiency
Overmolding enhances cost efficiency by reducing the need for secondary operations and assembly processes. By molding directly around the insert, it streamlines production, saving both time and labor costs. Additionally, it minimizes the risk of part failure associated with separate components, further contributing to overall cost savings.
Advantages of Overmolding and Insert Molding
Both overmolding and insert molding offer distinct advantages, making them suitable for a wide range of applications. Here’s a comprehensive overview of the benefits of each process:
Insert Molding
Insert molding excels in creating strong and durable connections between different materials. Its advantages include:
- Robust and Reusable Connections: Ideal for forming reliable bonds between plastic and metal or other materials.
- Cost Efficiency: Integrates components in a single molding process, reducing overall costs.
- Thin-Walled Production: Capable of manufacturing thin-walled cases that cannot be tapped.
- Reduced Assembly Requirements: Minimizes the need for additional part assembly, thus streamlining production.
- Enhanced Material Integration: Strengthens the performance of plastic-metal combinations by ensuring a secure bond.
- Increased Resilience: Produces components resistant to pull-out forces, vibration, moisture, and dust.
Overmolding
Overmolding offers significant benefits for improving product functionality and performance:
- Enhanced Material Flexibility: Uses multiple plastic materials to increase product flexibility and performance.
- No Need for Additional Joining Methods: Eliminates the necessity for welding or adhesive bonding, simplifying the manufacturing process.
- Improved Durability: Boosts product durability and overall performance.
- Strong Material Bonding: Creates a robust connection between different plastic materials, ensuring a cohesive and reliable final product.
By leveraging the strengths of both overmolding and insert molding, you can achieve superior results tailored to your specific project needs.
Application Of Silicone Overmolding
Overmolding is a technique that enhances a product's tactile quality, functionality, or aesthetics by integrating different materials. For example, it can combine a metal frame with a plastic housing for electronic devices. If a product requires a soft, ergonomic grip or improved user comfort, overmolding is an ideal solution.
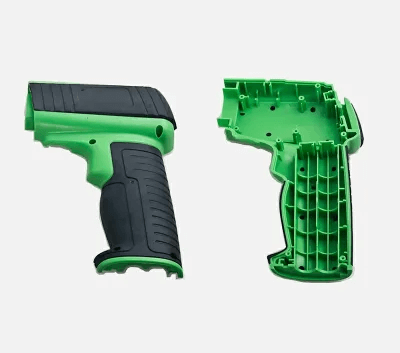
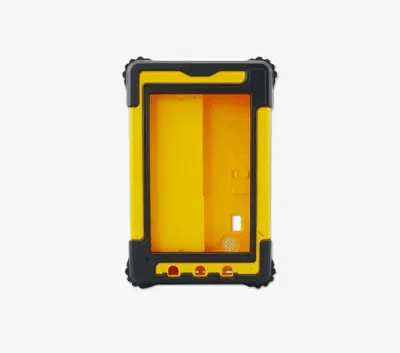
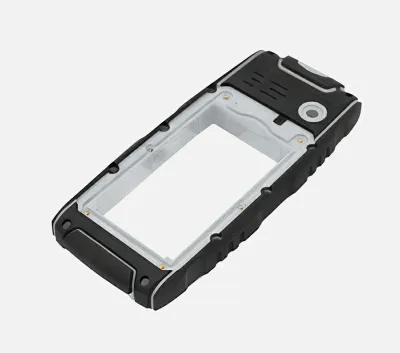
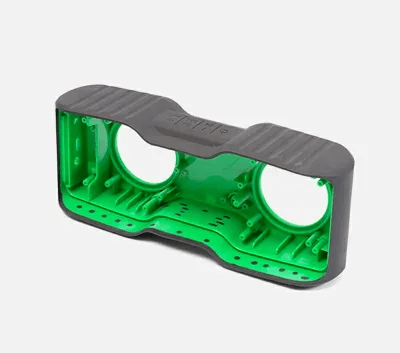
Applications of Insert Molding
Insert molding is a process designed to produce parts with intricate geometries or to combine multiple components into a single assembly. For instance, it can integrate a metal frame with a plastic housing for electronic devices. This technique is particularly advantageous when a product requires an insert for structural reinforcement or electrical conductivity, making it the optimal choice for such applications.
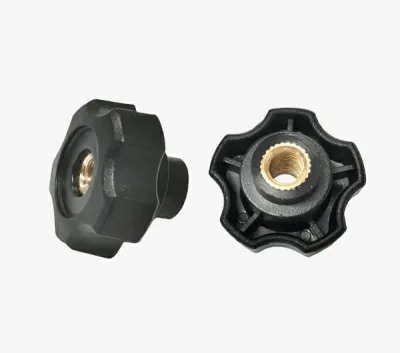
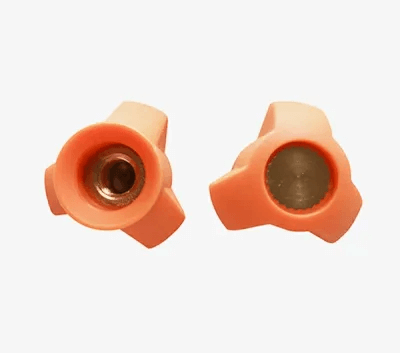
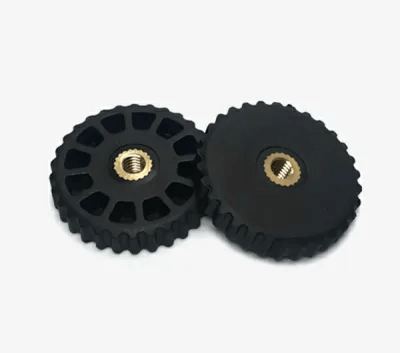
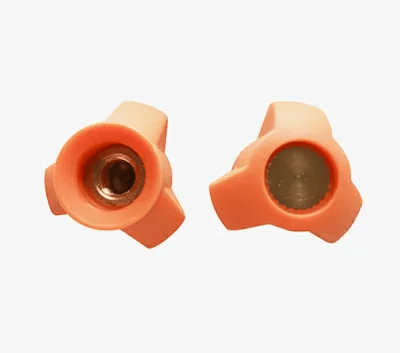