What is Plastic Injection Molding?
Plastic injection molding is the most efficient and cost-effective method for mass-producing plastic components. The process involves injecting molten plastic into a mold, where it cools and solidifies into the desired shape before being ejected. Using the same mold for each part ensures consistent quality across the entire production run. Compared to CNC machining and 3D printing, injection molding offers the greatest versatility in materials, colors, finishes, and surface textures.
Siliconebase's custom plastic molding service provides on-demand prototyping and production solutions tailored to your specific needs. Our customer-centric approach ensures we manufacture parts to your exact specifications without compromising on design or quality, all at a competitive price. Each injection mold quote includes expert consultation, and we assign dedicated project managers to oversee your order, ensuring a smooth transition from design to production. Our team possesses extensive experience across various industries, with particular expertise in medical injection molding and liquid silicone rubber (LSR) molding.
We have a wealth of experience in numerous sectors, especially in medical injection molding and the overmolding of plastics and liquid silicone rubber (LSR).
Plastic Injection Molding Capabilities
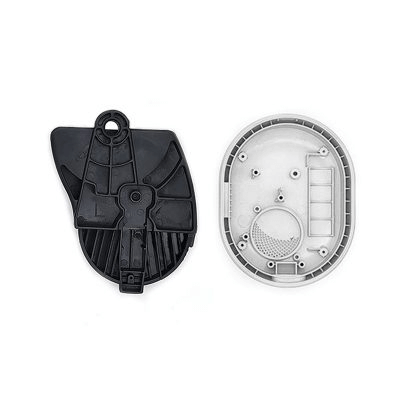
Injection Molding
The injection molding process accommodates a wide variety of resin materials. Plastic resin is heated to a molten state and then injected into a pre-designed metal mold. As the resin cools and solidifies, it takes on the shape of the mold, forming the desired component. Our engineers offer a range of raw material options, tailored to meet your specific needs.
Overmolding integrates multiple materials into a single component, enhancing product features such as UV resistance, chemical resistance, and impact resistance. This process also reduces the costs associated with assembly. Due to the different shrinkage rates of various materials, achieving precise mold accuracy is crucial.
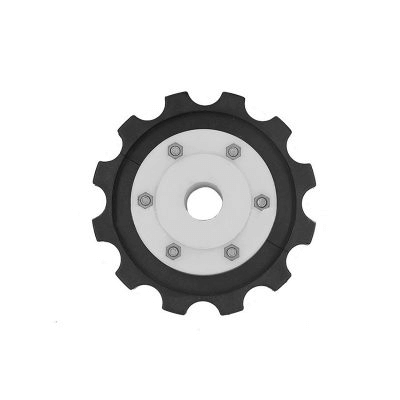
Insert Molding
Insert molding improves the mechanical properties of a component by inserting a preformed part into a mold and then overmolding it with plastic to create a unified piece. This process eliminates the need for additional components to connect various parts, thereby increasing assembly efficiency and reducing costs.
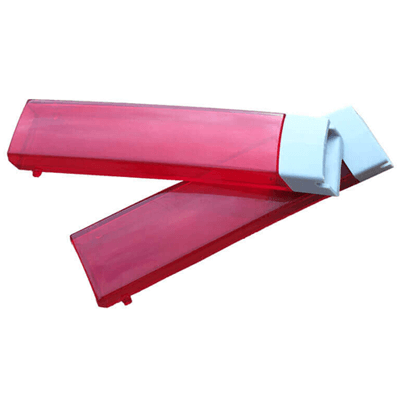
Plastic 2-Shot Molding
Two-shot injection molding, also known as dual-material or two-color injection molding, involves injecting two different materials into the same mold to produce a single, integrated part. This advanced manufacturing technique allows for the creation of components with distinct materials, which can vary in color or hardness. The result is an enhanced product in terms of aesthetics and performance, offering improved functionality and a refined appearance.
Our Injection Molding Advantages
Comprehensive Services
Siliconebase provides a full spectrum of injection molding services to global clients. Our team of skilled designers and engineers delivers cost-effective solutions supported by a robust management system, ensuring the timely production of high-quality products.
Rapid Turnaround
We offer expedited custom services with a streamlined process, including product design, DFM review, and prototyping, completed within 10-15 days. Our transparent production process and sample availability ensure that you achieve your desired product efficiently.
Exceptional Quality
Our organizational structure prioritizes excellence, with a rigorous quality assurance process for all raw materials. Our procurement team meticulously evaluates material quality to guarantee that we deliver superior products and exceptional service.
Versatile Applications
We work with nearly 200 different thermoplastic resins to produce injection-molded parts. Our capabilities include two-shot molding, overmolding, and insert molding, enabling us to create components with various colors and hardness for diverse applications in household, medical, electronic, and industrial sectors.
Plastic Injection Molding Process
We specialize in delivering high-precision and complex plastic components within a reduced timeframe. The plastic injection molding process is straightforward and efficient, enabling the production of custom prototypes and end-use parts within 15 days. The injection molding machine consists of three main components: the mold, the injection unit, and the clamping unit. Here’s an overview of the steps involved in customizing your plastic products through this process:
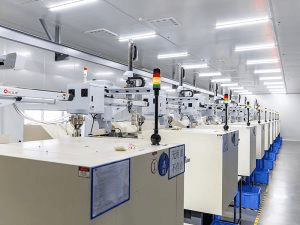
Step 1: Injection Molding
Thermoplastic resins are loaded into the barrel of the injection machine by our operators. The material undergoes melting, compression, and is then injected into the mold under controlled conditions to form the desired shape.
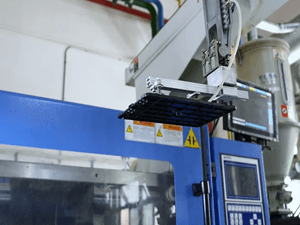
Step 2: Demolding
Once the thermoplastic resin has cured in the mold, it is cooled to solidify. After cooling, the mold is opened, and the finished parts are ejected into a collection bin.
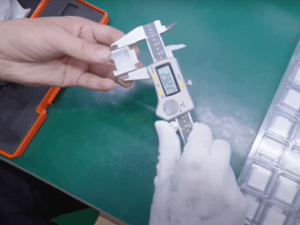
Step 3: Deflashing
Our quality control team inspects each part using advanced testing equipment to detect any imperfections such as rough edges. These are carefully trimmed to ensure the final products are smooth and meet high standards of cleanliness and quality.
Our Plastic Injection Capabilities
Service | Details |
Lead Time | Our services offer fast quote responses with design-for-manufacturing (DFM) feedback within 5 business days. |
Production Options | Domestic and international |
Machines Available | We provide a wide range of molding options, including single, multi-cavity, and family molds, with press tonnage capabilities ranging from 60 to 1,300+ tons. |
Inspection and Certification Options | Includes FAI, FMEA, and PPAP. ISO 9001,, ISO 16949, UL, Class 8 Medical Clean Room molding. |
Tool Ownership | Customer-owned with mold maintenance |
Mold Cavity Tolerances | a tolerance of +/- 0.005mm during mold machining while considering the shrink rate. |
Part to Part Repeatability | +/- 0.01mm or less |
Critical Feature Tolerances | Our company ensures critical features are milled to a steel-safe condition for optimal precision.. |
Available Mold Types | Single-Cavity Molds, Multi-Cavity Molds, Family Molds, and the production cycles will be under 1000 cycles, under 100,000 cycles, under 500,000 cycles and over 1000,000 cycles |