What Is Post-molding Processing?
Post-molding processing refers to the various processes and operations that occur after a product has been molded, transforming the raw molded parts into the final finished product. Post-molding processing is a critical stage in the manufacturing process, playing a significant role in determining the quality, functionality, and appearance of the end product.
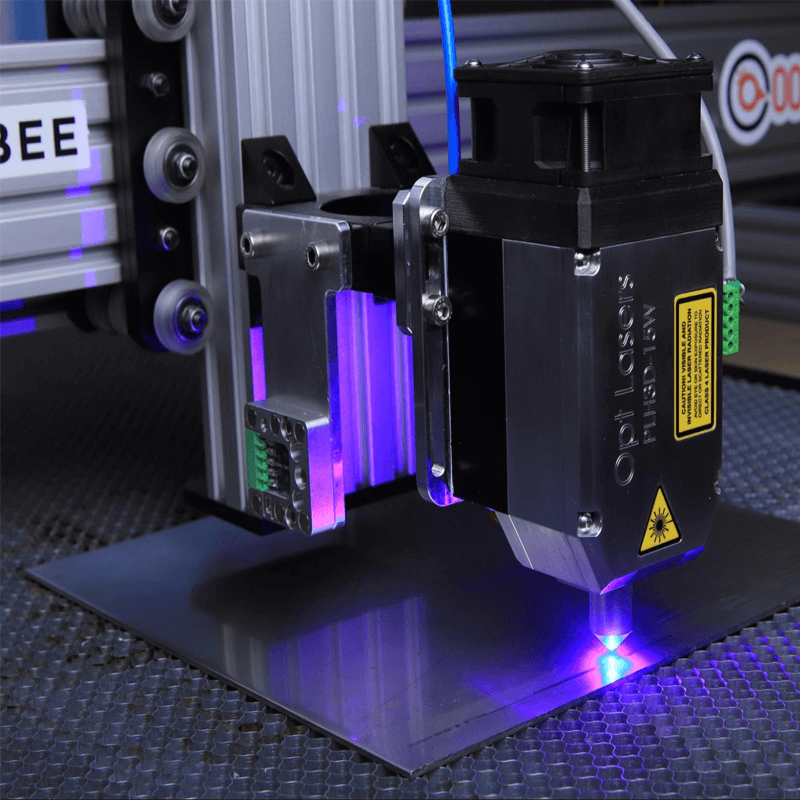
For Plastic and Silicone Post-molding Processes
Some of the Key Operations We Focus on Include:
Trimming and De-flashing: We use automated trimming and de-flashing processes to remove excess material or flash around the edges of the molded parts. This step helps in achieving the desired final shape and improves the overall aesthetics.
Inspection and Quality Control: Our automated inspection systems ensure that each part meets the required quality standards. Defective parts are promptly identified and sorted out, minimizing waste and ensuring that only top-quality components reach the customers.
Assembly: In cases where multiple plastic or silicone parts need to be combined to create a final product, we employ automated assembly systems. These systems ensure precise fitting and alignment, reducing assembly time and errors.
Surface Finishing: Post-molding, we also automate surface finishing processes such as polishing, painting, or applying coatings. This enhances the appearance and functionality of the parts as per the customer's specifications.
Packaging: Our automation extends to packaging as well, where we use automated systems to sort, package, and prepare the finished parts for shipment. This step streamlines the logistics process and ensures that products reach customers securely and in an organized manner.
Post-molding Processing for Silicone Parts
Post Curing: it is a process that occurs after molding LSR and silicone products. It creates strong molecular bonds within the material, improving compression set and reducing gas volatility. To accelerate curing, a post-curing method involving an oven, typically heated to 200°, is used. This ensures efficient and effective production of high-quality parts.
Silicone Oil Coating:
It enhances the surface smoothness, providing a delicate feel and eliminating any astringent sensation after molding.
The oil adds friction resistance and wear resistance, prolonging the service life of the silicone products.
By reducing static electricity, it helps prevent dust absorption during the rubber refining and forming processes.
Various surface effects of hand oil are available, such as frosted, mist, or glossy finishes. Customers can choose from common or high wear resistance types, as well as high or low-temperature curing options, depending on their product needs.
When applying hand oil, it is crucial to maintain an appropriate environment, preferably dust-free, with controlled temperature (20 ~ 30℃) and humidity (55 ~ 75%). These measures ensure proper leveling, adhesion, and film quality, avoiding potential issues like shrinkage, electrostatic dust pollution, and safety risks.
Screen printing
Silicone products are versatile but require various processing steps to become finished goods. Screen printing is a crucial process for many silicone products as it offers several advantages. It ensures clear and durable printing with good flow and viscosity, maintaining stability in high and low temperatures and resisting aging. Screen printing enhances the product's appearance with three-dimensional patterns and a pleasing texture. It also provides excellent peel strength, wear resistance, and brightness, contributing to improved performance and aesthetics of the final silicone products.
Laser engraving
Laser engraving is a highly versatile and efficient surface treatment process used for marking words or patterns on various materials. Compared to traditional methods like screen printing and pad printing, laser engraving offers numerous advantages, such as high-speed marking, beautiful images with high resolution, wear-resistant results, wide application range, safety, reliability, and consistent effects. It can be divided into dot matrix engraving and vector cutting methods.
In recent years, laser engraving technology has gained popularity in the printing field due to its ability to work with diverse materials like plastic, rubber, metal, and silicon wafers. It outperforms traditional methods like mechanical engraving and chemical etching by offering low operating costs, superior flexibility, precise control, easy operation, and permanent markings.
Treatment of Post Molded Parts
Post mold part treatments are done to a product following a custom plastic injection molding project to improve the plastics’ or product’s performance or quality.
Plastic Annealing
The process of heating or chemically treating a plastic product to relieve internal stresses and prevent dimensional shifts.
Moisture Conditioning
Hygroscopic plastics can become brittle after molding due to moisture absorption. Moisture conditioning rehydrates the plastic parts, restoring toughness and reducing stiffness.
Fixturing
Heavy-weighted or thick plastic products tend to retain excess heat during injection molding, leading to long cycle times or dimensional warping. To prevent this, storing the plastic parts in a fixture after molding allows them to cool off while maintaining their shape.
Enhance Your Post-Molding Processing with Siliconebase
At Siliconebase, we specialize in comprehensive post-molding processing to refine and perfect your injection-molded parts. Our services include a variety of surface finishes, from SPI standard textures to custom aesthetic touches like texturing, color matching, and design transfer.
We also offer advanced post-processing options such as part joining, durability enhancement, painting, light assembly, and protective packaging.
Our goal is to ensure your injection-molded components are not only highly functional and durable but also visually impressive. Let our skilled team guide you through the post-molding process and add the perfect final touches to your project. Contact us today to discover more about our post-molding services and discuss your specific needs.