How Compression Molding Works
Compression molding is a straightforward process, akin to making waffles. First, a specified amount of un-vulcanized silicone is placed into a mold cavity. Through the application of heat and pressure, the silicone is forced to fill and conform to the mold's contours. Once the parts have cured, they are carefully removed from the mold. This versatile technique can accommodate various processing requirements. Based on the specific usage and characteristics of your products, we will recommend an optimal production plan tailored to your needs.
Step 1: Material Preparation and Mixing
We begin by designing specific formulations tailored to your product’s application. Precise amounts of base silicone polymer and various additives are measured accordingly. These additives may include curing agents, catalysts, fillers, colorants, and other performance-enhancing substances. Using specialized equipment, the silicone polymer and additives are thoroughly mixed. This process enhances the product's properties, such as high-temperature resistance, flexibility, and electrical insulation.
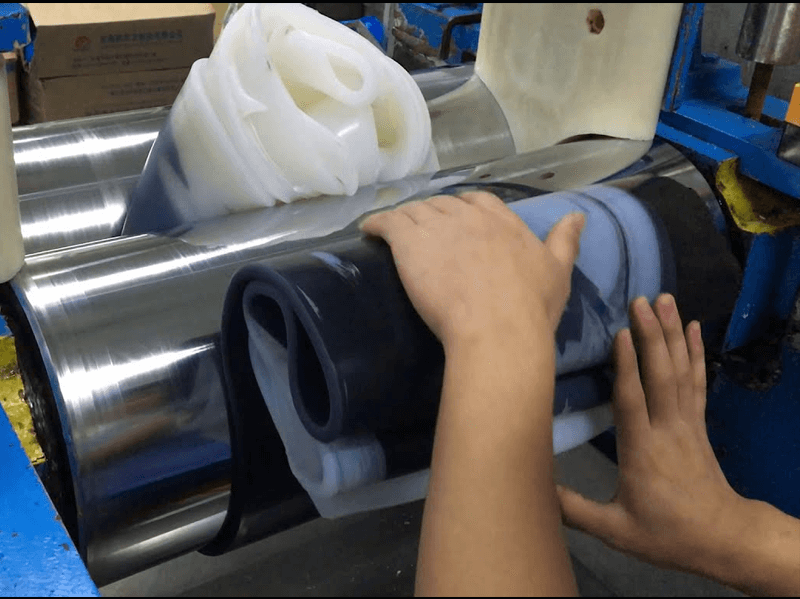
Step 2: Material Cutting
Our operators employ specialized mixing equipment to ensure the silicone and additives are evenly blended. To precisely control the weight of each molded product, we use cutting tools or machines to slice the material into uniform strips.
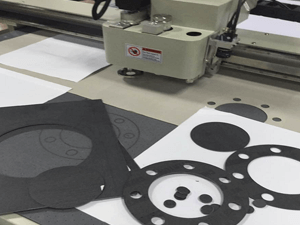
Step 3: Material Weighing
The pre-cut silicone material is weighed with precision to ensure the exact amount is used for each product. These precise measurements guarantee product consistency and quality.
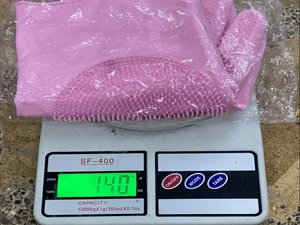
Step 4: Vulcanization Molding
Following the material cutting, the pre-cut silicone is placed into a preheated compression mold, which is then closed. Heat and pressure are applied to the material, initiating the curing process. The combination of compression and elevated temperature enables the silicone to solidify into the mold's shape.
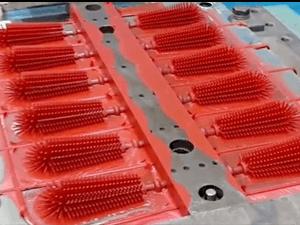
Step 5: Demolding and Trimming
Once the products have cooled, they are carefully removed from the mold, with attention given to prevent any damage. Excess material, or flash, is then trimmed away. Our quality control team thoroughly inspects each product for defects to ensure that only high-quality items are delivered to you.
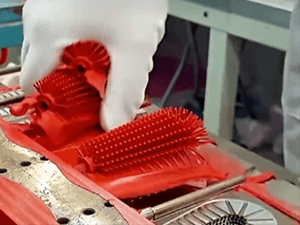
Compression Molding Capabilities
Single-Shot Molding
In single-shot molding, a single type of silicone is utilized throughout the process. This method is commonly employed for producing silicone keypads, silicone ring seals, and other similar products.
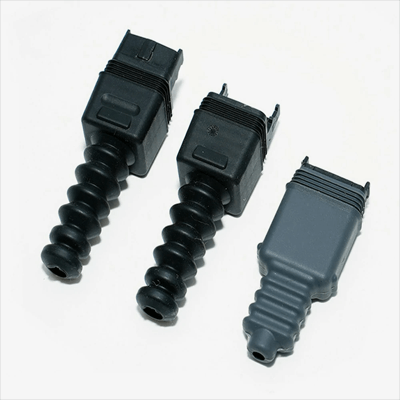
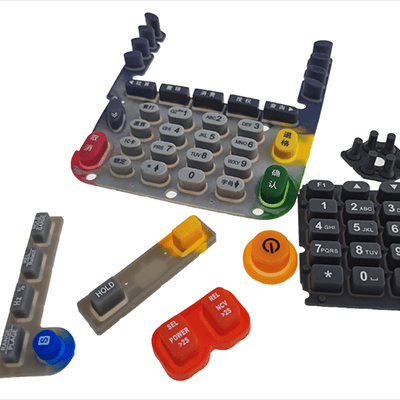
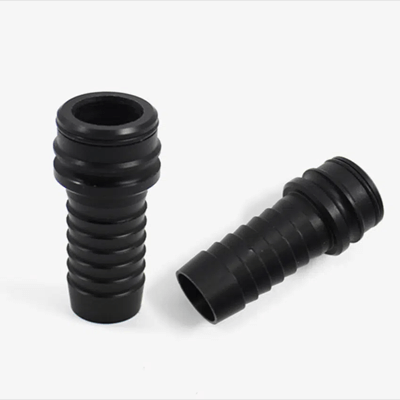
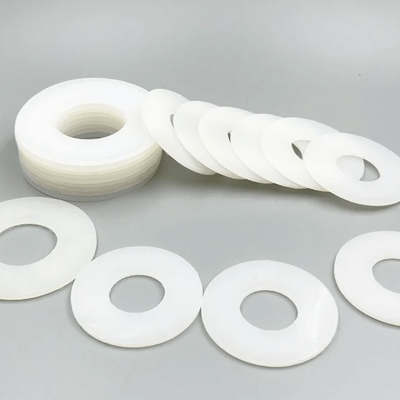
Silicone Overmolding
Silicone and Metal Combinations
This combination is ideal for applications that demand high hardness and excellent water resistance, such as SIM card holders, charging cable interfaces, and power buttons.
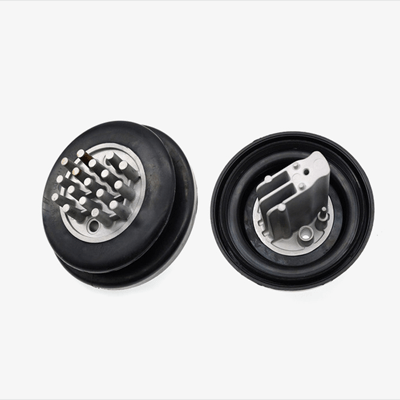
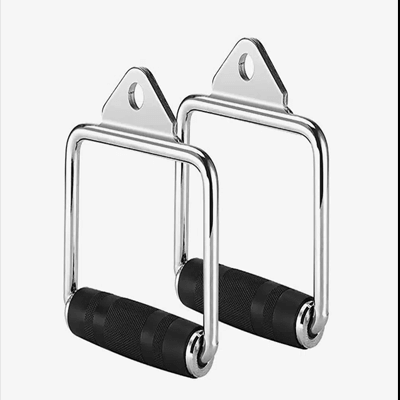
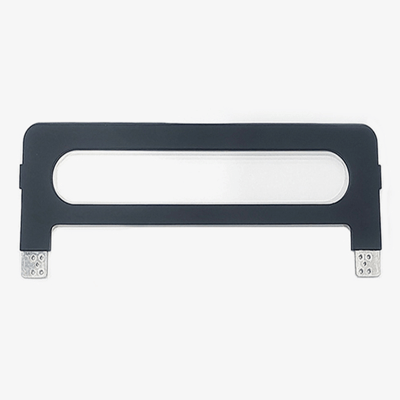
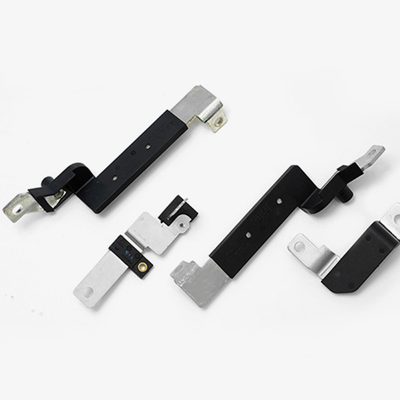
Silicone and Plastic Combinations
Combining silicone with plastic enhances product firmness and vibration resistance. This approach is widely used in applications such as electronic interfaces, Bluetooth audio covers, and mobile phone cases.
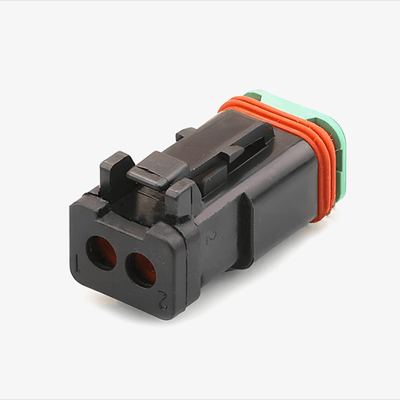
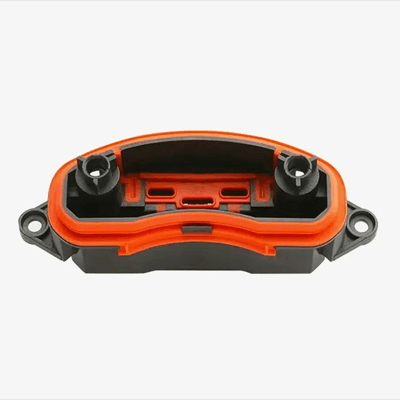
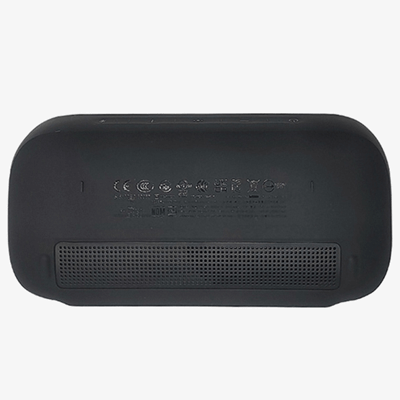
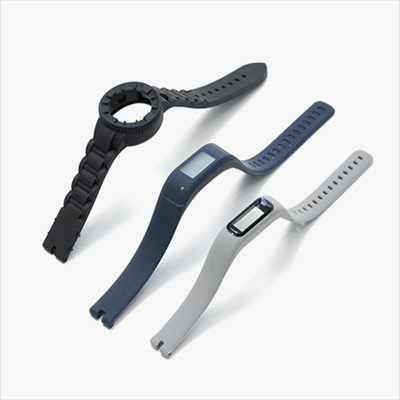
Advantages of Rubber Compression Molding
Cost-Effective
Compared to Liquid Silicone Rubber (LSR) injection molding, compression molding involves simpler equipment, easier operation, and more affordable raw materials. This results in lower capital investment and reduced production costs, especially for straightforward parts.
Efficient High-Volume Production
The process is both simple and efficient, allowing for the design of multiple cavities within a single mold. With nearly 60 molding machines at Lan Xin, we are well-equipped to handle large-scale production.
Rapid Mold Production and Lower Costs
Our experienced mold development team can deliver prototypes within 7-10 days, expediting your development cycle and offering competitive mold pricing.
Versatile Processing Capabilities
Silicone compression molding supports single-shot molding and can integrate silicone with various materials such as metal, plastic, PET, and fabric into a single component, accommodating diverse application needs.
Silicone Compression Molding vs. Liquid Injection Molding
Cost-Effectiveness
Compression molding is more cost-efficient than liquid injection molding due to its simpler mold design and the capability to produce multiple cavities with less expensive tooling.
Rapid Mold Production
Compression molding offers faster mold production times, typically 15-20 days, with simpler parts sometimes taking just 7-10 days. In contrast, liquid injection molding requires a longer lead time of 40-55 days for mold fabrication.
Ease of Maintenance
The straightforward structure of compression molds simplifies maintenance and setup. Setting up a compression mold generally takes about 1 hour, while liquid silicone injection molds require approximately 1 day for assembly.
Material Versatility
Compression molding supports a broad range of materials, particularly those that maintain flexibility after curing. It is suitable for thermosets and can accommodate multiple cavities. Common materials used include silicone, natural rubber, and EPDM.
High Production Capacity
Compression molding machines are designed for high production volumes, enabling efficient mass production. The ability to incorporate multiple cavities in a single mold enhances output compared to injection molding methods.
Color Testing Flexibility
Compression molding allows for easier color testing. The mold can be cleaned and reloaded with colored silicone for different tests. In contrast, liquid injection molding requires more time (typically about half a day) to clean the color system and needles, leading to time and material wastage. Consequently, liquid injection molding is less suited for frequent color changes.