Mold Design And Making
At Siliconebase, we bring decades of expertise in tooling design, including plastic and LSR injection molding, over-molding, silicone compression molding, and silicone and plastic extrusion. We adhere to ISO 9001 and IATF 16949 standards, consistently surpassing customer expectations.
Our skilled in-house tool and die makers, equipped with CNC capabilities, efficiently craft new molds. We offer cost-effective Reaction Injection Molding (RIM) solutions, providing a range of molds that balance cost and tool longevity, aligning with your project’s requirements and budget.
Our advanced tooling capabilities excel in producing high-quality, durable, heat-resistant, and non-toxic silicone products. Manufacturers partnering with us can be confident in delivering kitchen products that stand out for their exceptional quality and reliability.
Why Choose Siliconebase For Your Tooling Manufacturing Needs?
At Siliconebase, we leverage advanced equipment, customized design, and engineering support to deliver high-precision, efficient tooling solutions that meet the dynamic needs of the kitchenware industry.
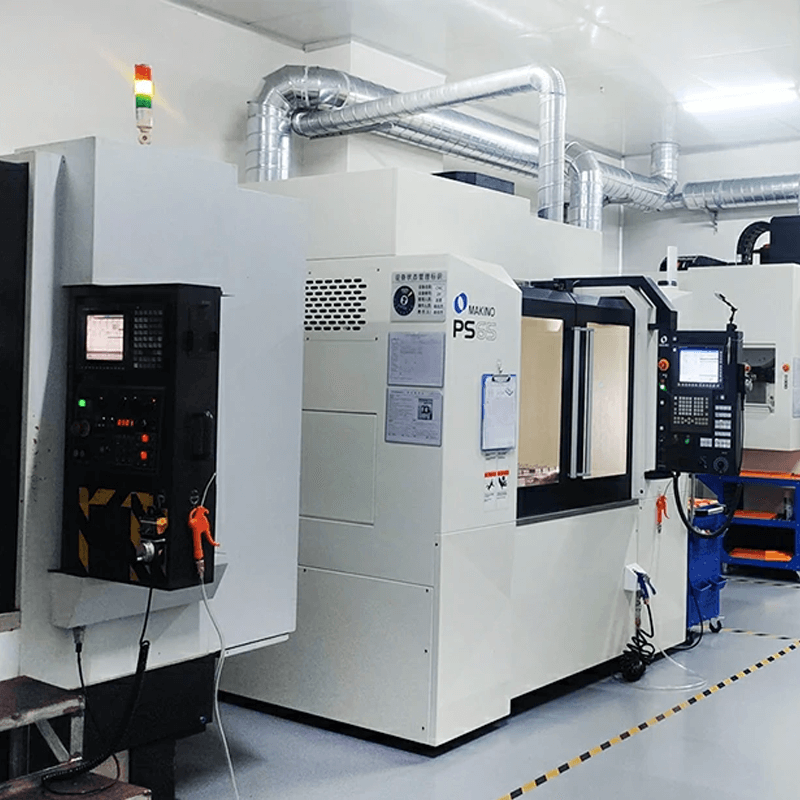
Advanced Equipment and Technology
Our facility is equipped with state-of-the-art manufacturing equipment, including high-precision CNC machines, CAD/CAM software, and 3D printing technology. This enables us to achieve precise tooling manufacturing and create intricate and complex shapes with exceptional accuracy.
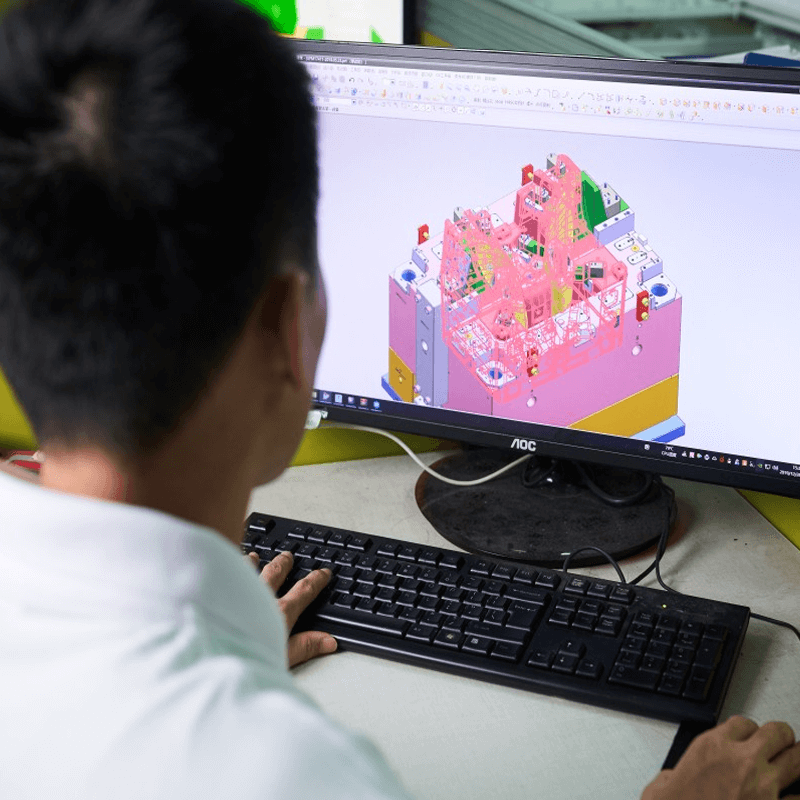
Customized Design and Engineering Support
We collaborate closely with our customers to understand their specific needs and silicone product requirements. Our experienced engineers provide expert design advice and engineering support, ensuring that the tooling design aligns with customer expectations and product specifications.
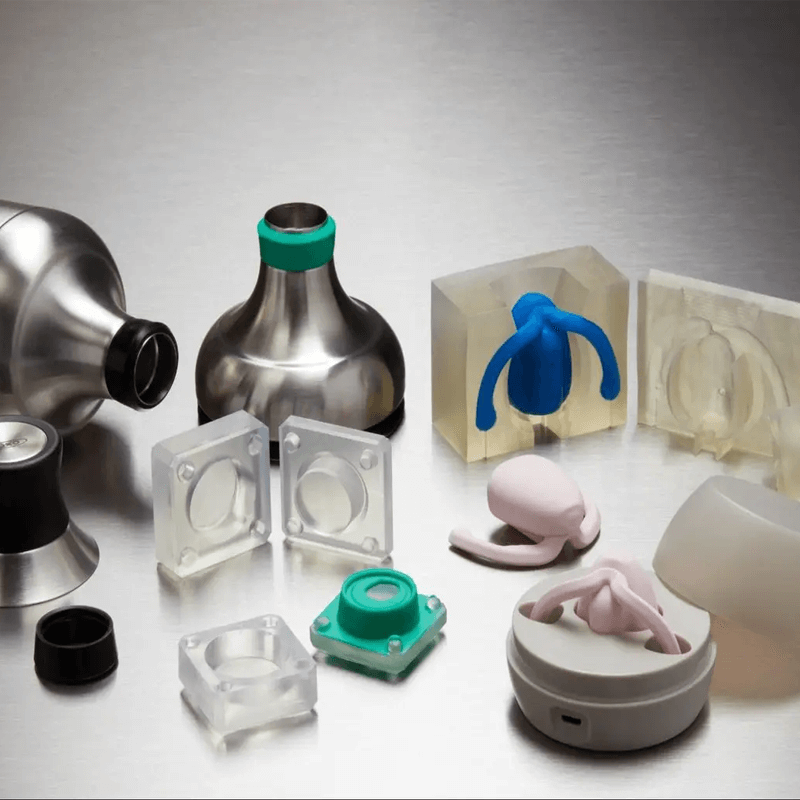
High-Quality Materials and Manufacturing Standards
We use premium-grade steel and wear-resistant alloys for our tooling, adhering to strict quality control standards. This commitment ensures each tool's manufacturing quality, consistency, durability, stability, and lifespan.
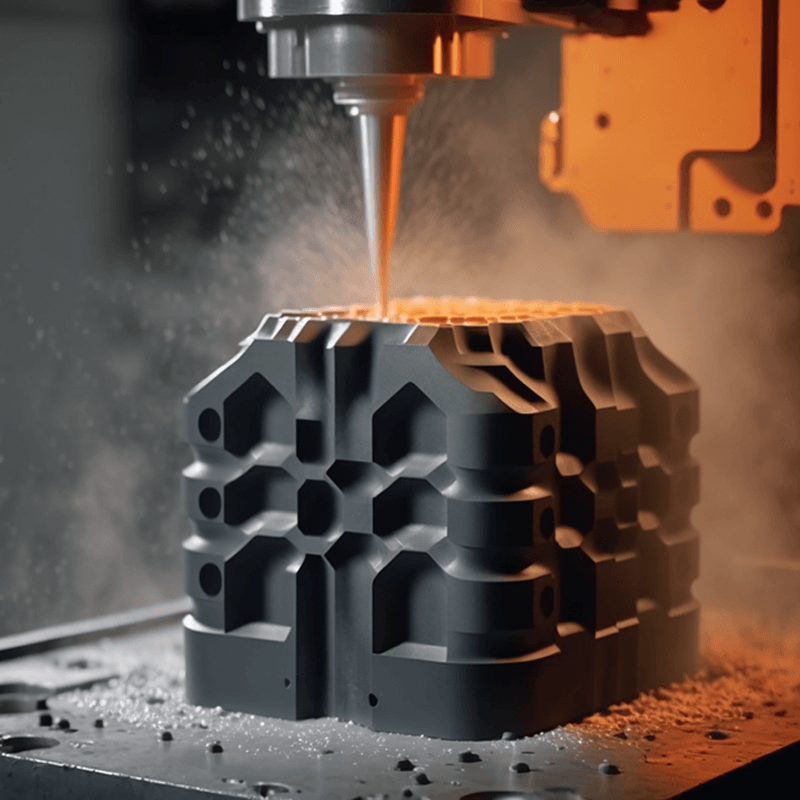
Technological Innovation and Continuous Improvement
Driven by innovation, we constantly explore new manufacturing methods and materials. By integrating advanced processes and technologies, we enhance the precision, complexity, and production efficiency of our tooling, keeping pace with market demands.
The Importance Of Material Selection In Tooling Design
Selecting the appropriate grade of steel is paramount in tooling design. Achieving the correct steel hardness is essential to balance wear resistance and toughness, ensuring that tooling components do not wear out prematurely. Given that tooling represents a significant expense in the injection molding process, we meticulously engineer them using a pro-injection mold metals comparison approach for tool design and materials. This ensures the tools have an extended lifespan and require minimal maintenance. Key factors to consider during this process include:
- Production Run Size: The volume of parts to be produced.
- Part Complexity: The intricacy of the part's design.
- Finish Quality: The level of surface finish required.
- Material to Be Molded: Some plastics are corrosive, while others contain abrasive glass fibers.
To achieve extended tool life and minimal maintenance, we prioritize using high-quality steel grades such as S136, S136H, and NAK80. These hardened steels are renowned for their exceptional performance, making them ideal for high-volume production and complex parts. By incorporating these superior materials, we ensure that our tooling delivers unparalleled durability and longevity, meeting the rigorous demands of the injection molding industry.
Common Types of Mold Steels:
- P20 (P20HH): A widely used pre-hardened mold steel known for good wear resistance and machinability, suitable for small to medium-scale production and simple parts.
- S136 (S136H): Stainless steel mold steel offering high hardness and corrosion resistance, ideal for high-production volumes and complex parts.
- NAK80: A high-hardness heat-treated mold steel, particularly suitable for high-gloss parts or molds requiring a mirror finish.
- H13: Hot work mold steel suitable for high-temperature applications, featuring excellent heat and wear resistance.
- 718 (718H): Premium wear-resistant steel suitable for medium to large-sized complex molds and high-volume production.
- 2738 (P20+Ni): Nickel-added pre-hardened mold steel, suitable for large injection molds and high-performance engineering plastics.
- 2316: Stainless steel mold steel with excellent corrosion and wear resistance, suitable for producing highly transparent injection molded parts.
These are some common types of mold steels. Different applications and requirements may necessitate selecting various steel types to ensure optimal performance and longevity.
Mould Making Process
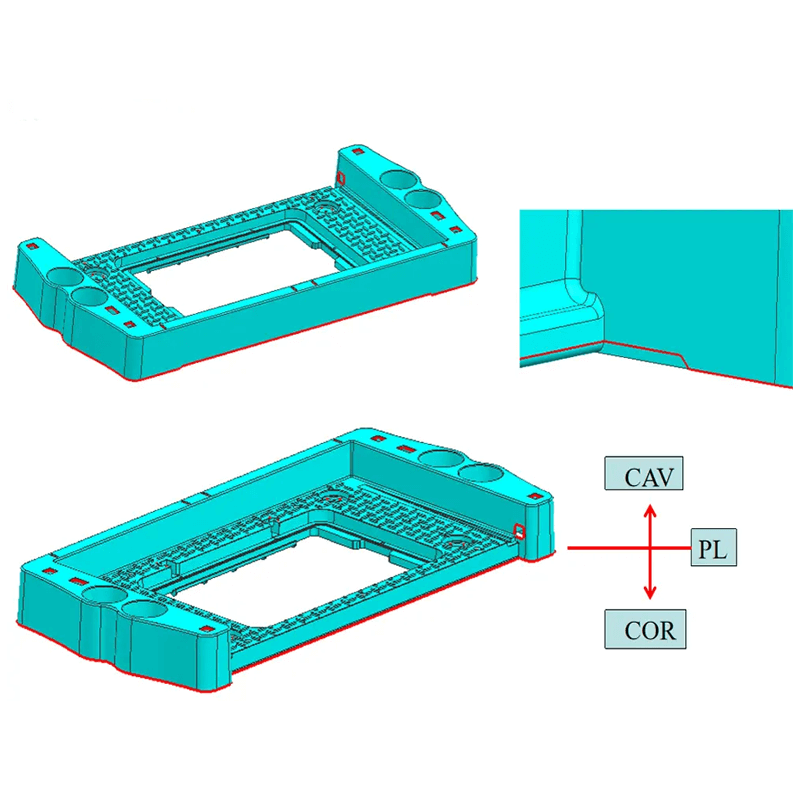
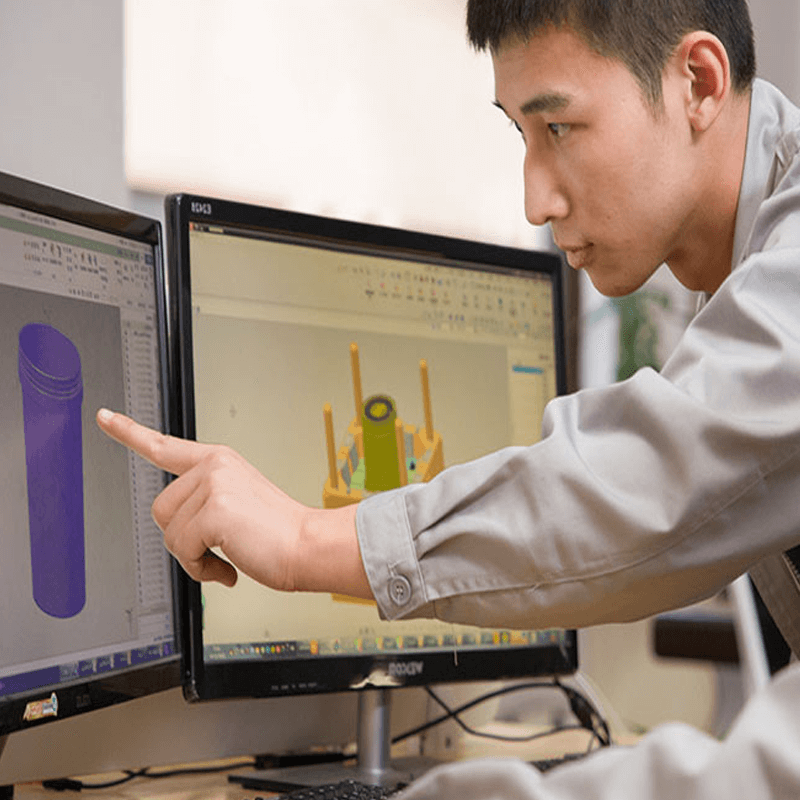
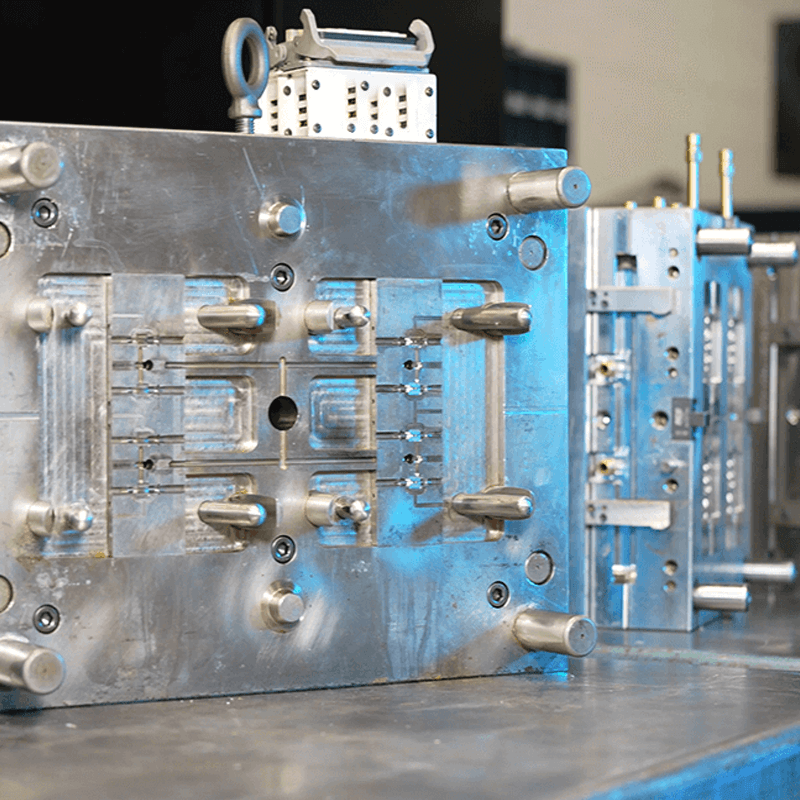
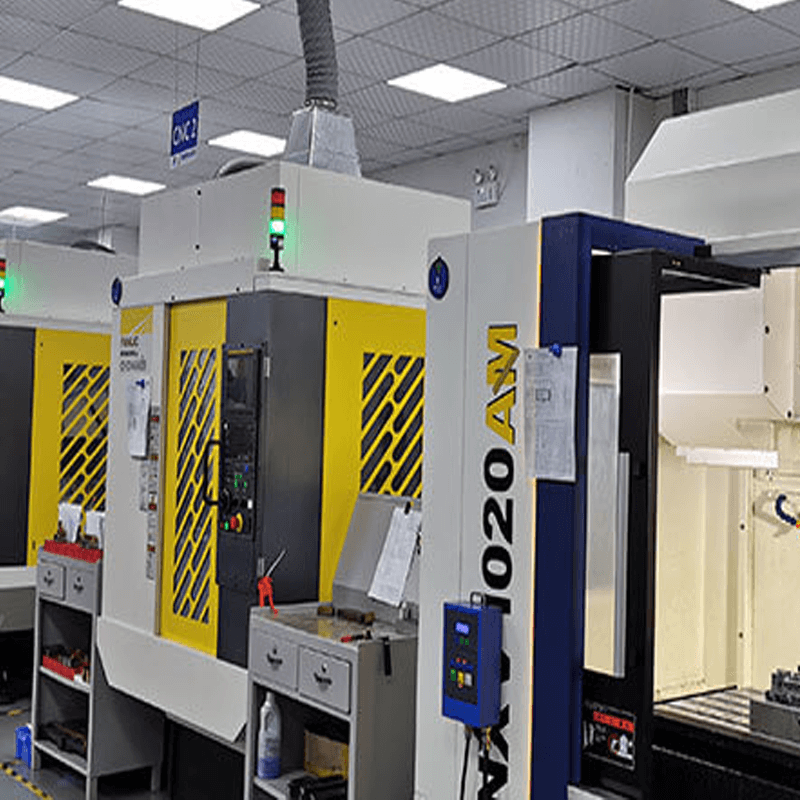
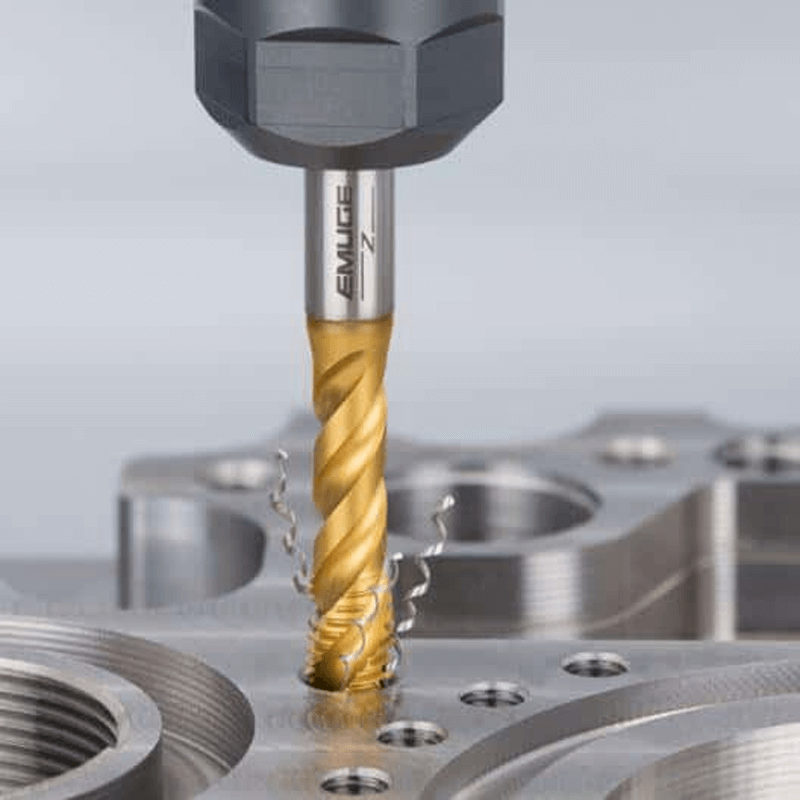
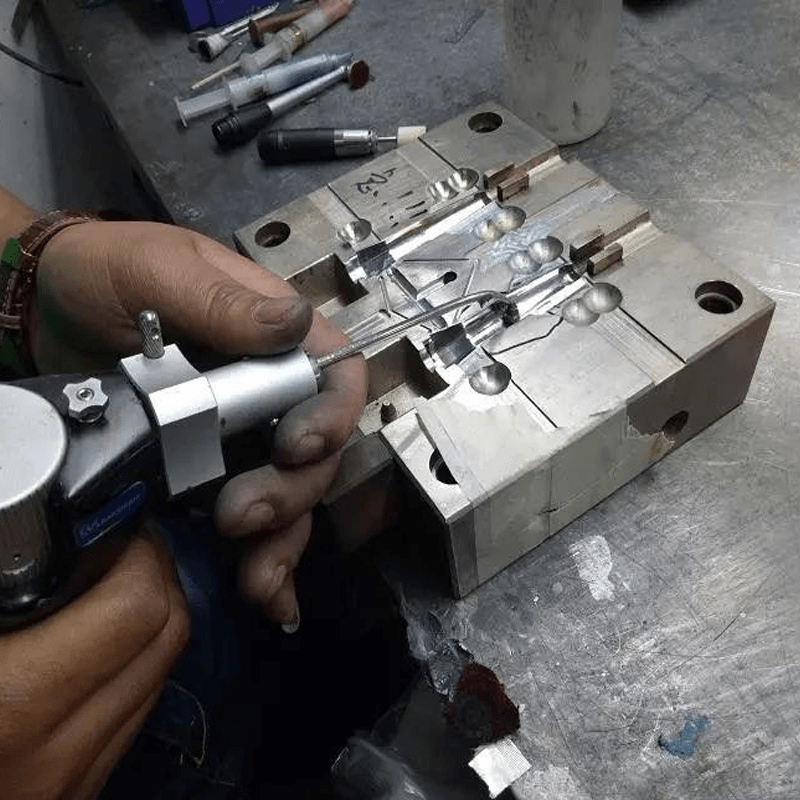
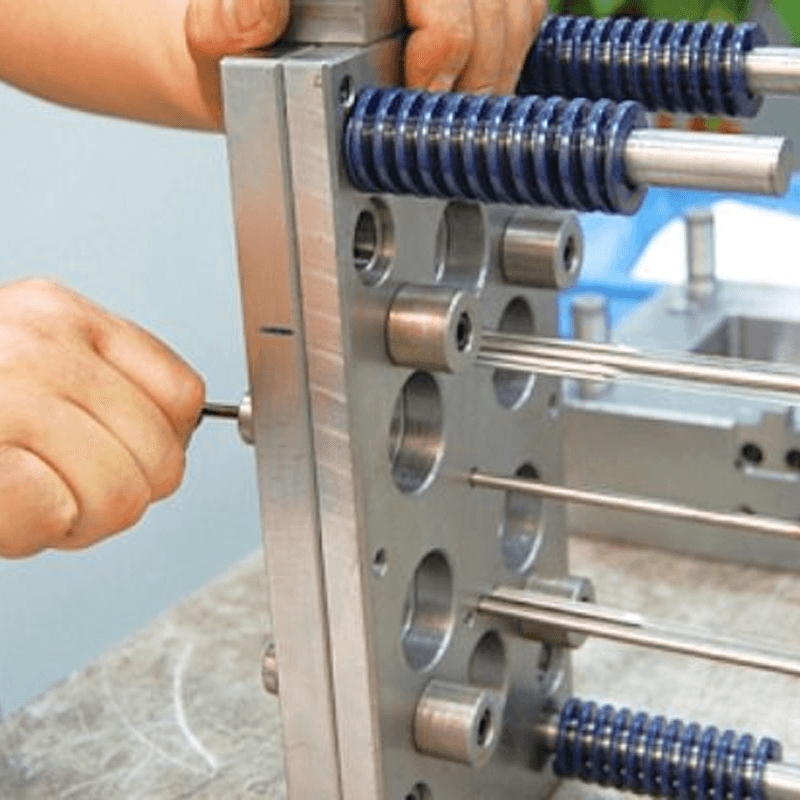
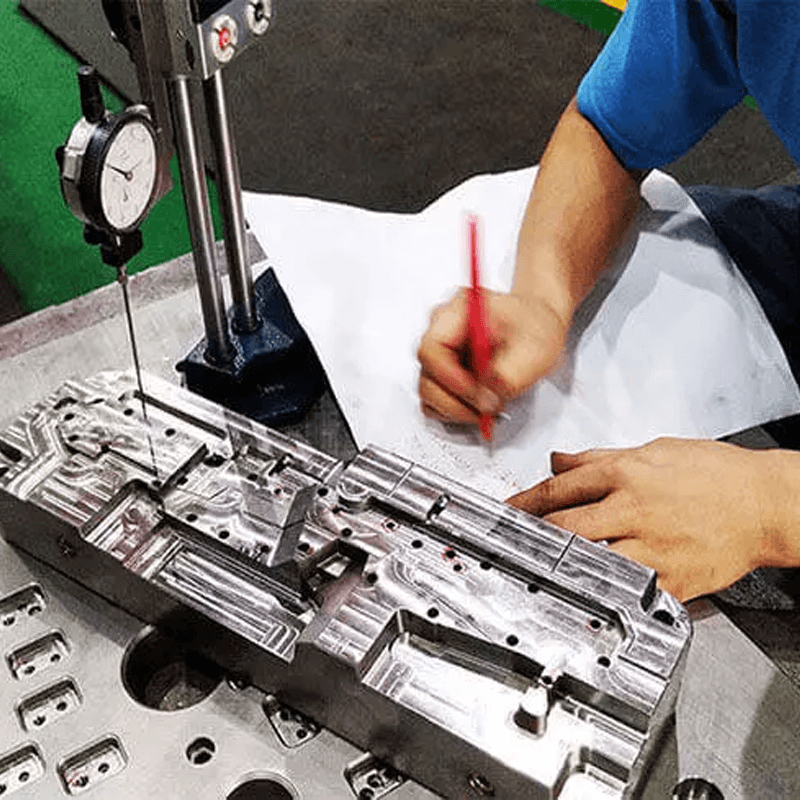
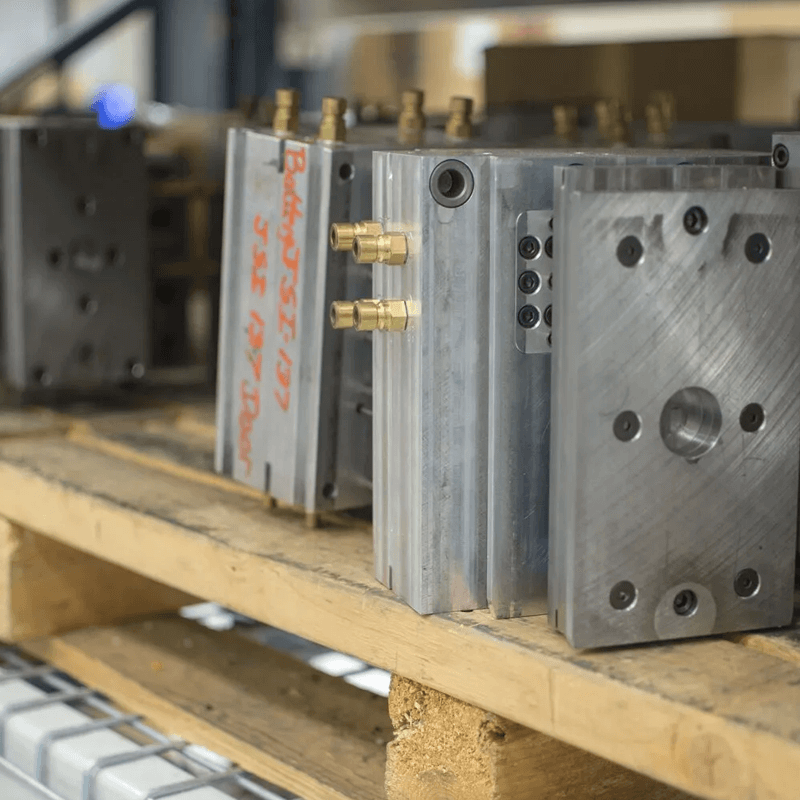
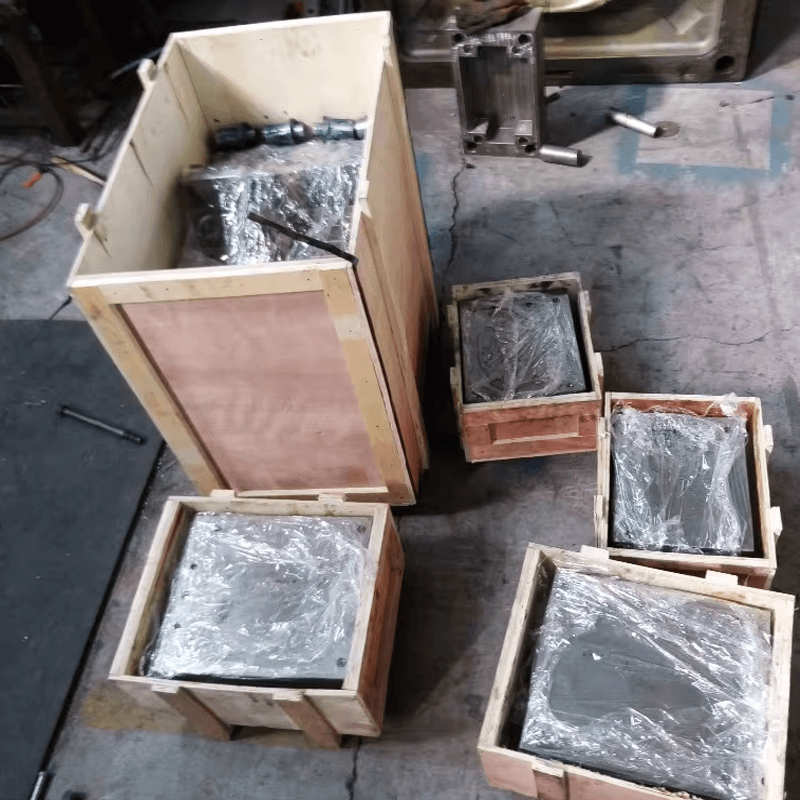
Surface Treatment Methods for Molds
Selecting the appropriate surface treatment for molds is crucial to ensure optimal performance and longevity. The choice depends on the mold material, its intended use, and the desired surface characteristics. Here are some common surface treatment methods:
Polishing: Polishing involves grinding and buffing the mold surface to achieve a smooth, glossy finish. This process enhances the mold's appearance and reduces friction and adhesion issues.
Coating: Applying protective coatings such as chrome plating, nickel plating, or titanium plating to the mold surface can significantly increase wear resistance and provide additional protection.
Spray Painting: This method involves applying specialized coatings or paints to the mold surface to alter its characteristics or provide protection. Examples include anti-corrosion coatings to prevent rust and anti-stick coatings to reduce adhesion.
Nitriding: Nitriding is a process where the mold surface is treated with nitrogen gas at high temperatures to form a hard nitride layer. This treatment increases the mold's hardness and wear resistance.
Electrical Discharge Machining (EDM): EDM creates micro-spark holes on the mold surface, improving surface quality and reducing adhesion issues.
Sandblasting: Sandblasting propels fine sand particles at high pressure onto the mold surface to remove dirt, oxides, and pits, thereby enhancing surface quality.
Heat Treatment: This method involves heating and cooling the mold material to alter its microstructure, increasing hardness and durability.